Examples of applications
The hardness increases significantly without having a negative impact on corrosion resistance.
See also the white paper, brochure and certificates:
The excellent corrosion resistance of austenitic stainless steels has led to a wide commercial use of these materials
The most well-known and widely used types of stainless steel are Aisi 316(L) and Aisi 304. But also other austenitic stainless steel variants due to their very good corrosion resistance and non magnetic properties are widely used in the automotive, oil & gas, chemical, medical and food industries.
An important disadvantage of austenitic stainless steel is its relatively low hardness, low wear resistance and sensitivity to galling (cold welding). This limits its use in high-end mechanical applications in various applications where these properties are very important.
The reason why a martensitic stainless steel is not chosen is that, although these materials have a significantly higher hardness and wear resistance, they have a much lower corrosion resistance.
In the past many attempts have been made to develop a hardening- or surface treatment technique which, without adversely affecting corrosion resistance, can improve wear resistance but also, for example, fatigue strength. Conventional processes such as nitriding, boronozing and coatings cannot provide in this.
For a number of years there has been a process at Aalberts Surface Technologies Eindhoven B.V. called Stainihard® NC. This process ensures a strong improvement of the wear resistance and the fatigue strength, but also prevents against the well-known “galling”. This while the corrosion resistance remains unchanged and in some cases is even improved.
It also offers advantages in places where machines need to be cleaned regularly. Here Stainihard® NC ensures that foodstuffs, such as milk products, stick less and can therefore be removed more easily and more quickly.
Generally said, it offers the industry an excellent solution when wear and galling resistance must go hand in hand with good to very good corrosion resistance.
In the industry there is a large variety of products and parts that will benefit from this treatment,
Some application examples are:
pump components of a twin screw pump
Example from the Food industry, where slurry-like substances such as ketchup, mayonnaise or for example chocolate are processed. In these substances, small hard particles (such as tomato seeds or cocoa chunks) can always cause a lot of abrasive wear. Also, at the start of a production run there is always the risk of “galling” of stainless steel on stainless steel is present. In this pump 2 or 4 screws, with a minimum gap space, rotate in the pump housing. Screws and housing treated with the stainihard process are able to resist this abrasive wear for a significantly longer time, resulting in a much longer life and also less production downtime.
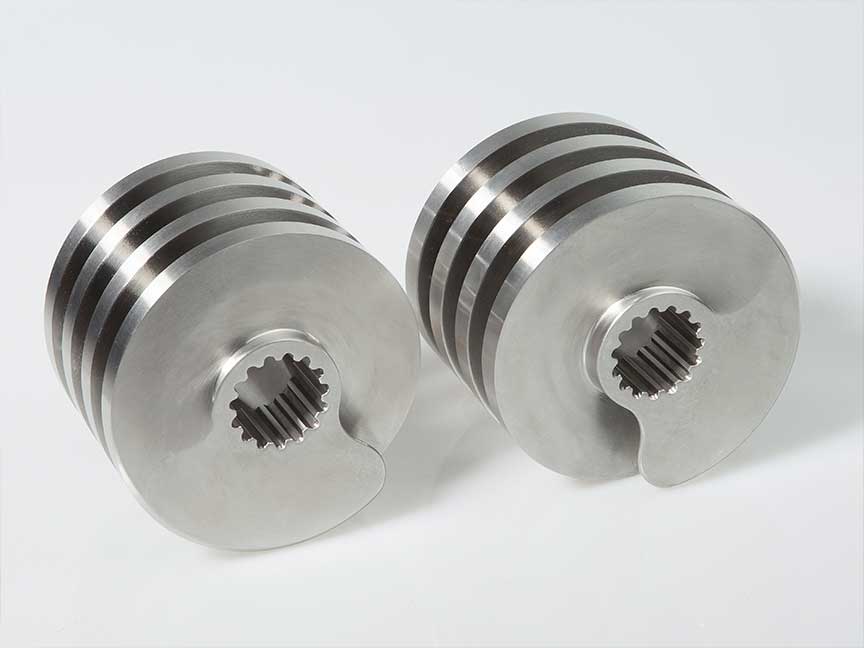
drive of a peeling machine
Example from the Food industry. Where asparagus used to be peeled and cleaned by hand, automated peeling machines are now being used more and more frequently. Because this is seasonal work, a drive with shafts made from regular steel has the great disadvantage of corroding. Partly due to the long standstill and the time that rust forms on these shafts, there is a high risk of malfunctions. Therefore is in this drive a stainless steel 303 chosen so that the corrosion resistance is guaranteed. Only now the problem arises that this material quickly starts to wear out strongly. By treating the shafts with the Stainihard process this excessive wear is avoided.
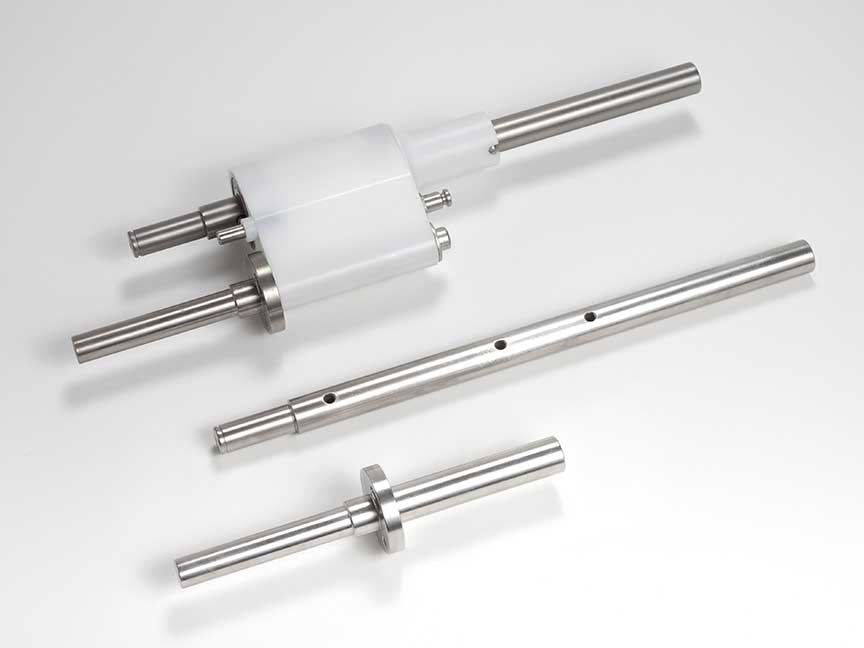
tube of electromagnetic valve for a automotive application
For a solenoid valve/switch to function properly, a stainless steel tube/bushing is needed between the copper winding and the soft iron core. One of the advantages of austenitic stainless steel compared to steel is its non-magnetic properties. The disadvantage, however, is that the soft iron core is harder and therefore the stainless steel housing will show excessive wear. With Stainihard it is possible to apply a wear-resistant zone even to the inside (even if it is closed at one end) of a product.These Stainihard-treated sleeves easily pass the prescribed lifetime test.t.
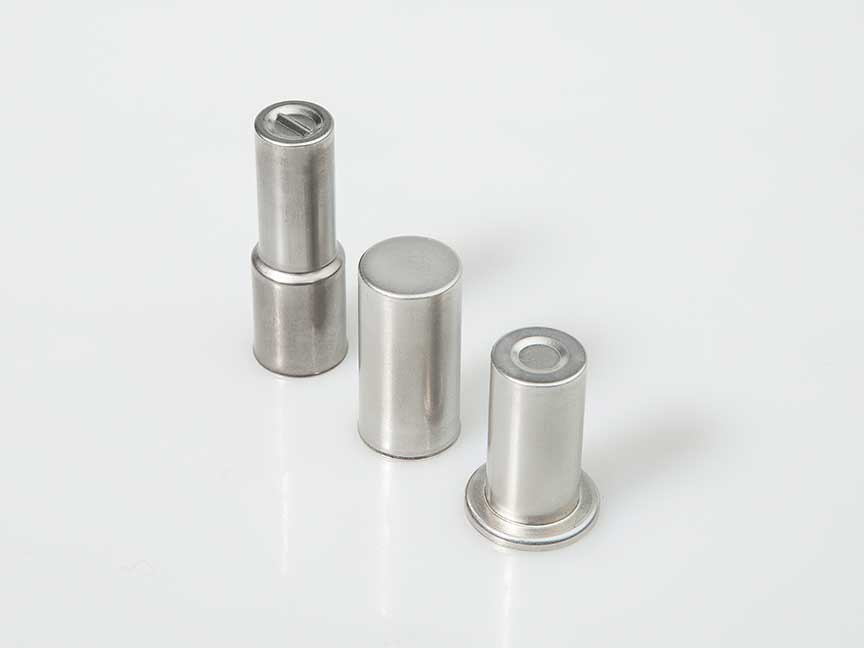
ferrules of a pipe-clamp fitting
This ferrule must be able to cut itself into the pipe and therefore needs a significantly higher hardness while on the “sliding side” the galling must be avoided. In the past, these were traditionally nitrided or carburized, with the result that the corrosion resistance no longer meets specifications. A salt spray test (DIN50021) shows that nitrided cutting rings show the first signs of corrosion after only 20 hours, whereas the stainihard treated cutting rings showed no signs of corrosion after 500 hours.
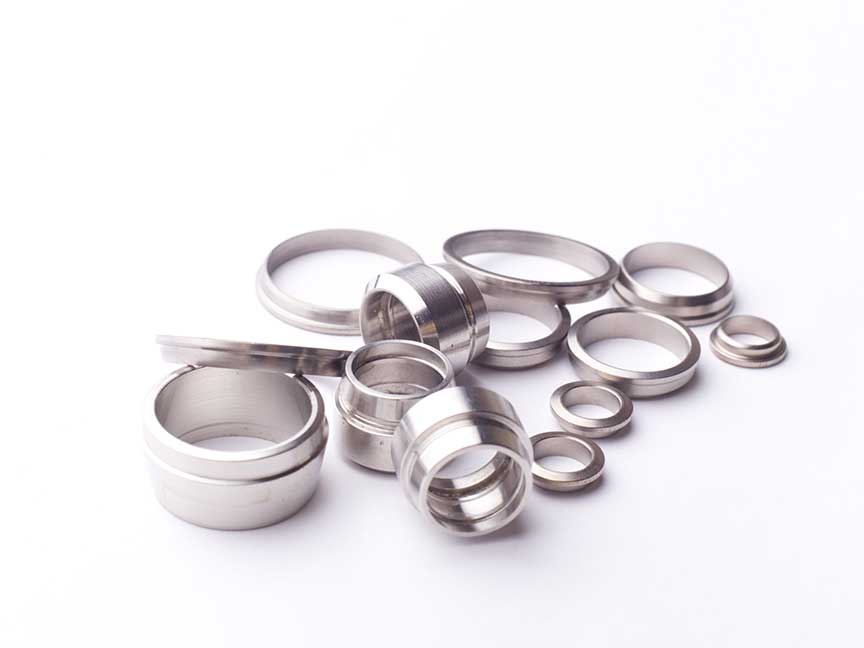